Numerical Simulation of Three-phase Flow in a Top-blown Converter with a 4-hole Oxygen Lance
-
摘要: 采用数值模拟软件Fluent建立了一个瞬态的三维数学模型,对100 t氧气顶吹转炉流场进行数值模拟。通过改变氧枪枪位和氧枪喷孔夹角,得出相应的冲击深度和冲击面积以及熔池内部速度分布。结果表明,在相同的条件下,随喷吹枪位的升高,射流形成的钢液凹坑直径变大,而冲击深度变小;随喷孔夹角的增大,射流冲击直径变大,而冲击深度减小。低枪位有利于增大熔池上层钢液流速,高枪位利于促进熔池下部钢液流动;喷孔夹角增大利于增大熔池表层高速区面积,但熔池中心底部低速区面积也随之增大。Abstract: A three dimensional transient mathematical model for the 100 t oxygen top-blown converter has been carried out using the numerical simulation software fluent.The impact depth,impact area and molten bath velocity distribution had been obtained at different oxygen lance height and oxygen lance nozzle angle.It is found out that under the same condition,raising the lance position leads to larger diameter of pit created by jets,while the impact depth decreases.As the nozzle hole cone angle increases,the diameter of pit created by jets become larger,while the impact depth decreases.Low lance position is beneficial to increase flow velocity of the liquid steel at the upper molten bath,while high lance position is conducive to promote the liquid steel flow of the bottom bath.Increasing the nozzle hole cone angle promotes the large high-speed surface zone area,but the low speed zone area at the bottom of the molten bath has been increased as well.
-
Key words:
- converter /
- three-phase fluid /
- flow field /
- oxygen lance /
- lance position /
- nozzle angle /
- numerical simulation
-
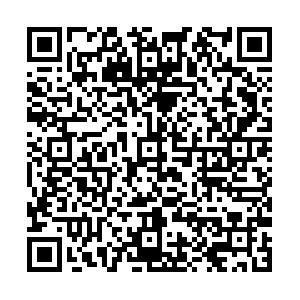
计量
- 文章访问数: 114
- HTML全文浏览量: 25
- PDF下载量: 2
- 被引次数: 0